What's the Best Wood Finish?
Understanding and selecting the right wood finish for your project
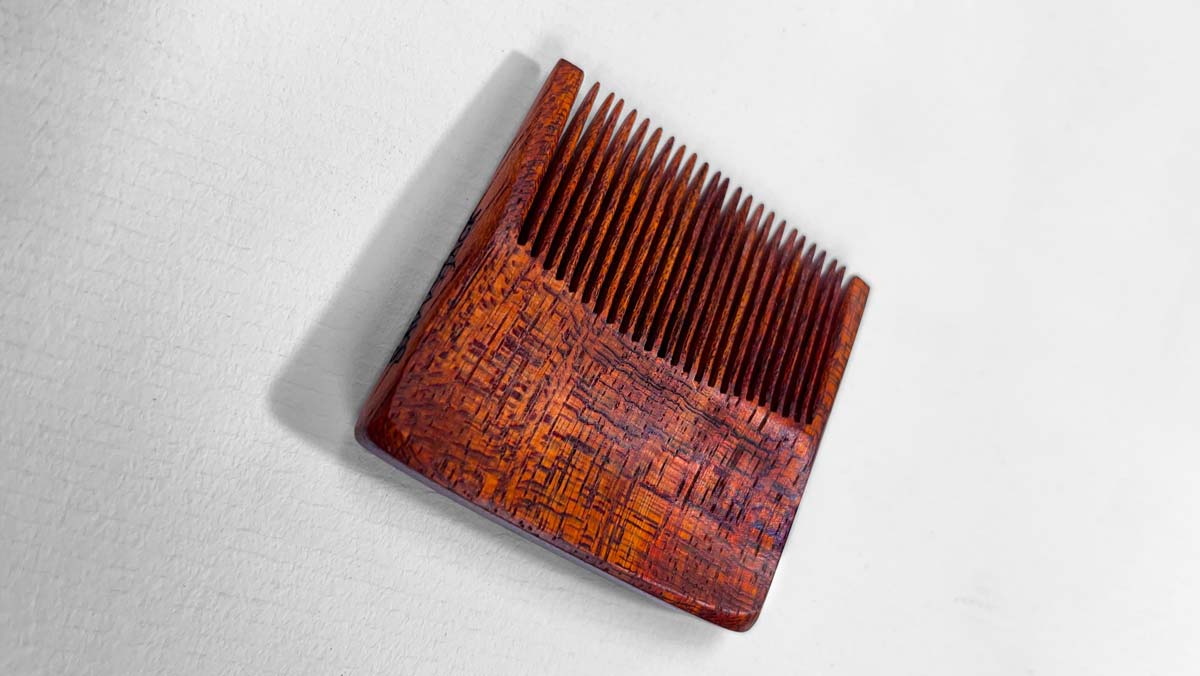
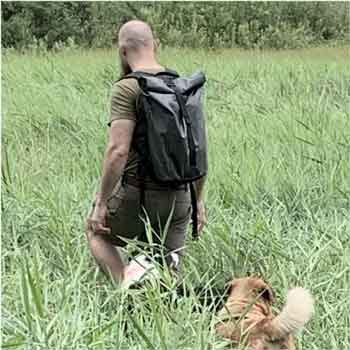
An exceptional wood finish, and what I use for all SavvyJack products:
-
Sutherland Welles Murdoch's Hard Oil
- A varnish made with polymerized Tung oil and uralkyd resin
-
Excellent Protection & Longevity
- It cures hard, providing excellent water resistance and overall durability.
- The substantial tung oil content reduces ridgidity. This provides the flexibility needed for wood that might get wet.
-
Versatile Sheen Level
- Varies by method of application and number of coats.
- Can target the optimal balance between protection and natural wood feel.
-
Long Open Working Time
- 20+ minutes
- Sufficient time to cover fairly large surfaces
- Forgiving in small areas like comb teeth, as it does not quickly gum up on the wood.
- Lacquer and water-based finishes don't provide as much protection as varnish, but their exceptional clarity better preserves the white color in woods like maple.
- Oils are too soft to build a film layer of protection—This also means that they can achieve the lowest sheen of any finish.
- Within each finish category, there are a range of formulations which themselves have tradeoffs to take into consideration.
Of course, I've tried a good number of finishes over the years...
That said, much of what I know about wood finishes is thanks to Bob Flexner and his excellent book, "Understanding Wood Finishing: How to select and apply the right finish." I highly recommend it.
Flexner has also written many useful Popular Woodworking articles available online in the Bob Flexner archive.
Choosing the right finish:
Generally speaking, harder finishes provide more protection, are less flexible and are glossier. That said, within each category, these properties vary widely.
Most wood finishes can be grouped into the following categories:
In my opinion, varnish has the best qualities for a great finish.
Most "oil" finishes sold today are not oil, but varnishes or oil/varnish blends.
They go by names like:
- Teak Oil, Danish Oil, Antique Oil and even Tung Oil
Though it's misleading, these are actually better finishes than a simple oil. But if you're looking for an oil, these aren't it.
*Each finish category has a "Quick Info" dropdown with the following:
-
Protection & Longevity
- Resistance to water, wear, heat, and solvents
- Finish flexibility
- Wood expands and contracts with changes in humidity. If a finish is too hard, it can't accomodate these changes without separation or cracking.
-
Appearance
- Matte, Satin, Gloss—Natural, Plasticky
- A high gloss finish is created by building a film layer on the wood surface.
- This enhances protection, but can look plasticky.
- The harder the finish, the better it can build layers.
-
Open working time
- How long before the finish begins to cure and becomes unworkable?
- Finishes with longer working times are more forgiving to poor technique.
- Larger surfaces require longer working times.
1. Varnish
A varnish is a combination of curing oil and resin—modified under heat.
Varnishes are the most protective wood finishes with excellent scratch, water, heat, and solvent resistance.
Varnish variations:
- Polyurethane, Varathane, Murdoch's Uralkyd 500
These varnishes have short working times. They build surface layers quickly. The final coat is often best diluted with solvent to attain a more level surface.
- Waterlox, Seal-a-cell, Formby's Tung Oil, Briwax Teak Oil
Bob Flexner coined the term "wiping varnish" to refer to varnishes that are diluted with solvents. This solvent content increases open working time, making them easy to apply—they can be wiped on and wiped off.
Wiping varnishes penetrate the wood more effectively, making them great first coatseven when using a full-strength varnish. As top coats, they provide better sheen control.
You can make your own wiping varnish by mixing full strength varnish with your choice of solvent.
Learn more about selecting and applying wiping varnishes.- Spar Varnish, Marine Varnish, Interlux Schooner
High-oil-content varnishes cure a bit softer. This is critical for outdoor environments that require a more flexible finish—like marine and high-humidity environments.
Outdoor varnishes also contain UV inhibitors so that they don't degrade as quickly in the sun.
- Watco Teak Oil, Minwax Teak Oil, Minwax Tung Oil, Danish Oil, Antique Oil
Oil/varnish blend = oil + varnish (no heat)
Varnish = oil + resin + heat
Oil/varnish blends cure softer than varnishes. Like high-oil-content varnishes, this is critical for outdoor environments that require a more flexible finish—like marine and high-humidity environments.
Oil/varnish blends have longer working times due to the oil content. Ratio of oil to varnish varies among brands.
Blends create a more matte finish than straight varnish.
My favorite varnish:
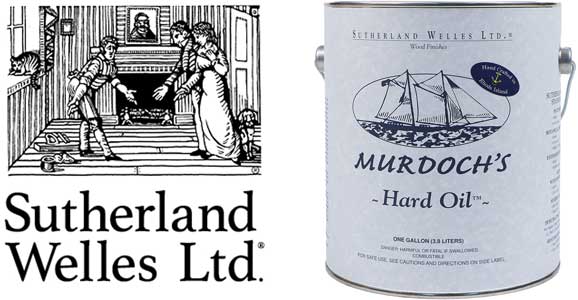
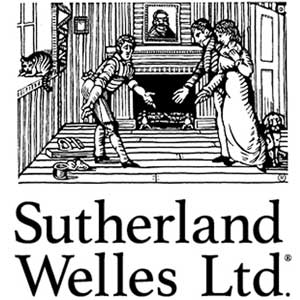
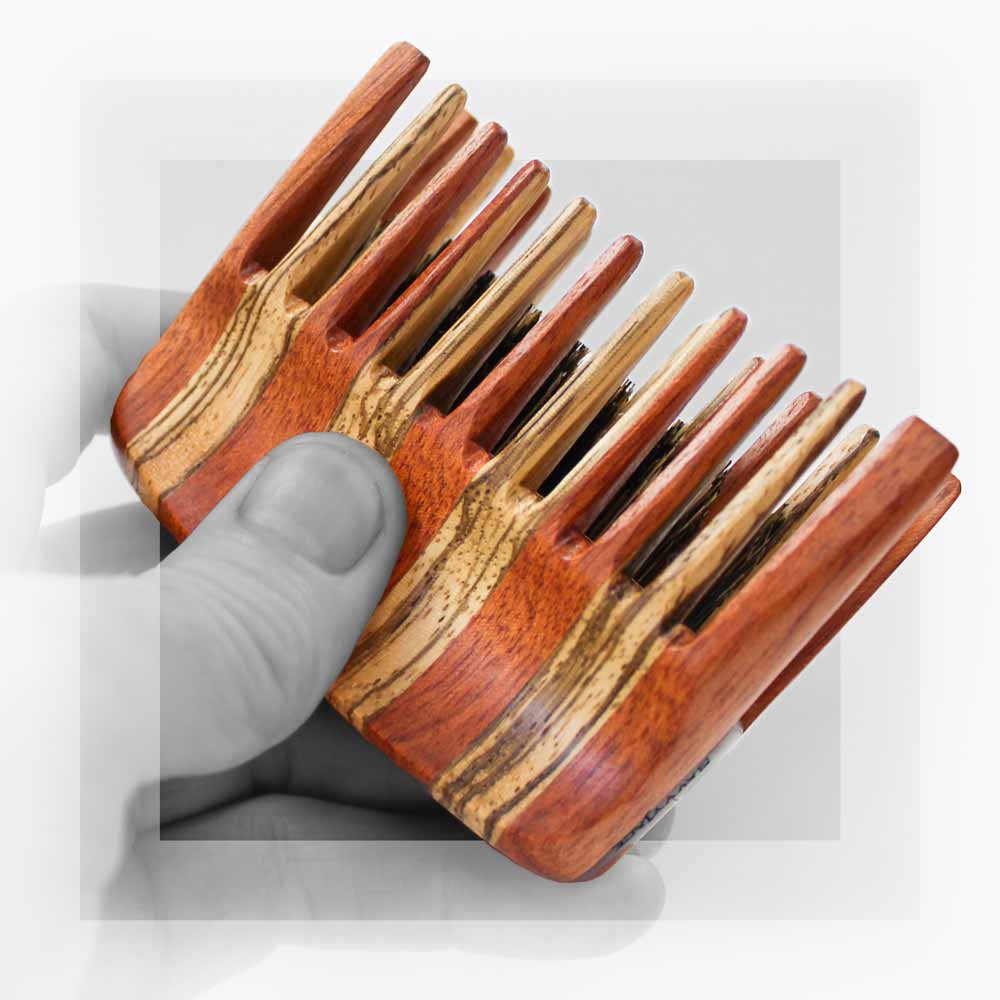
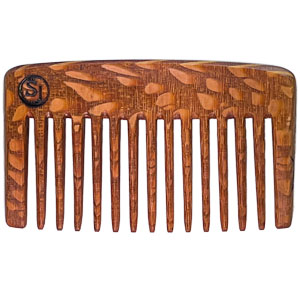
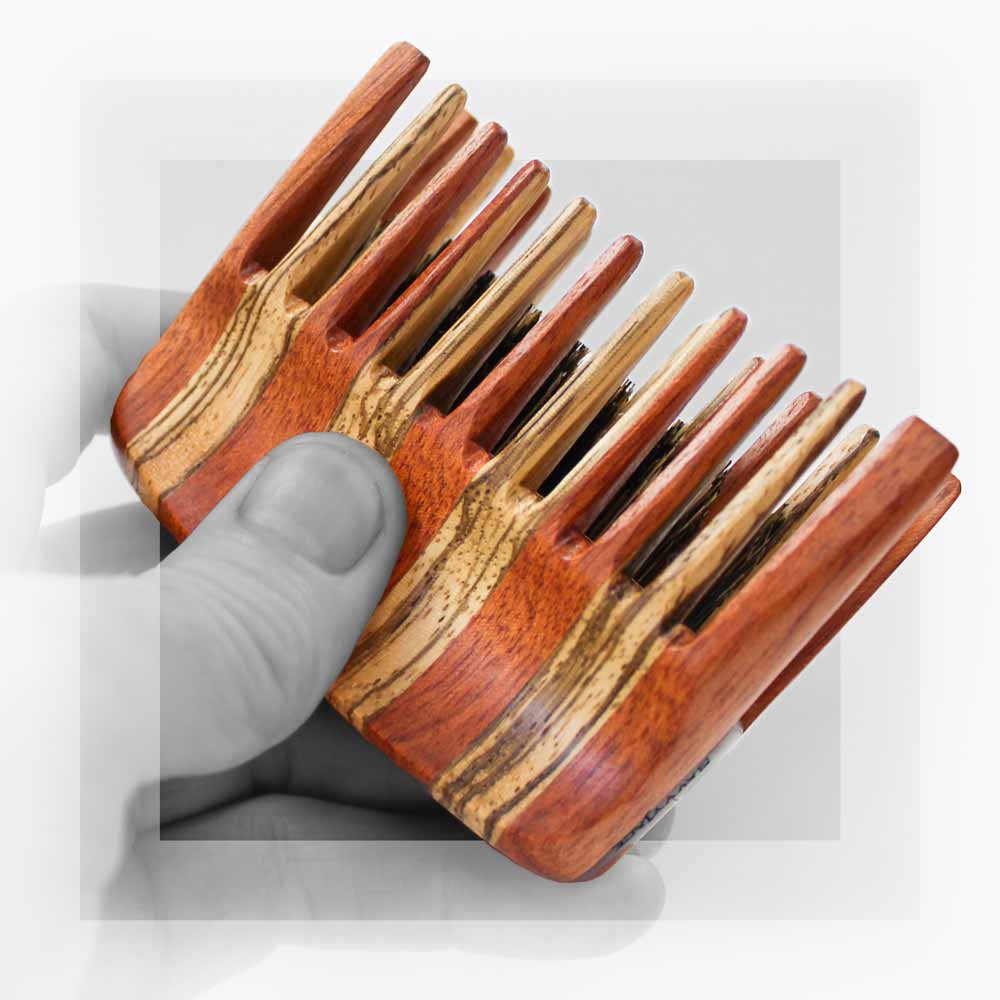
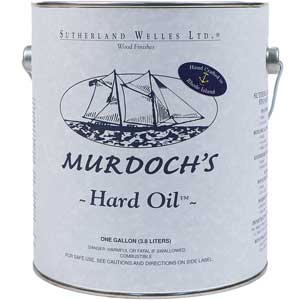
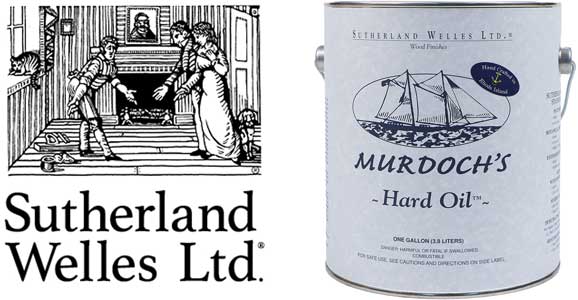
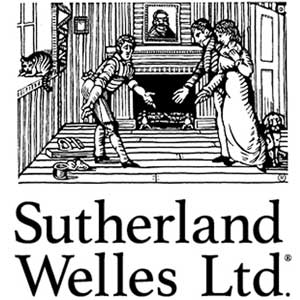
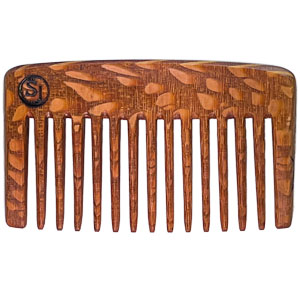
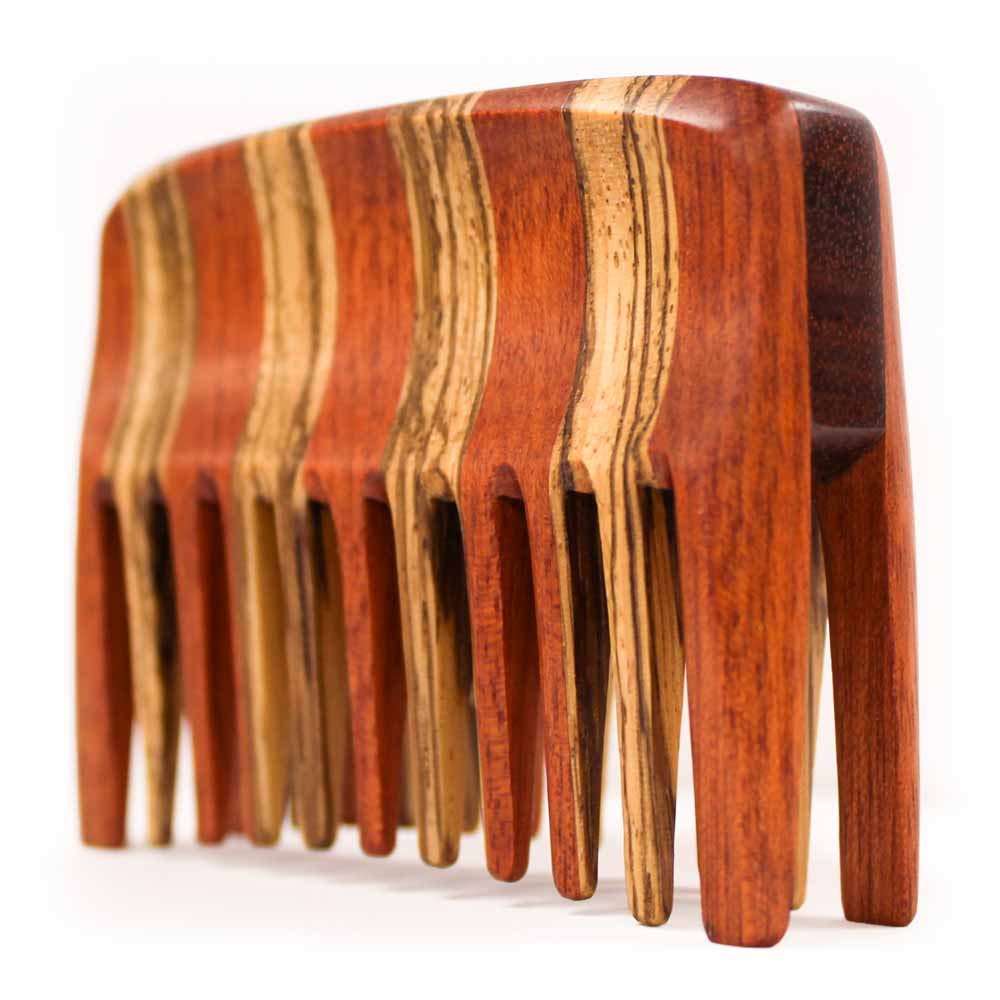
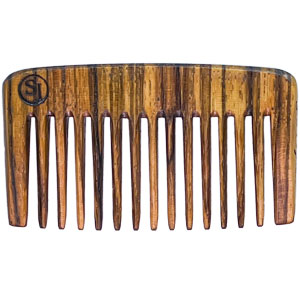
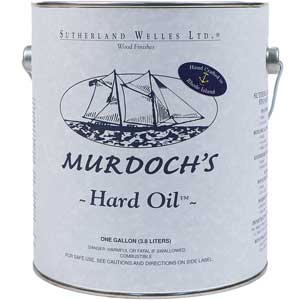
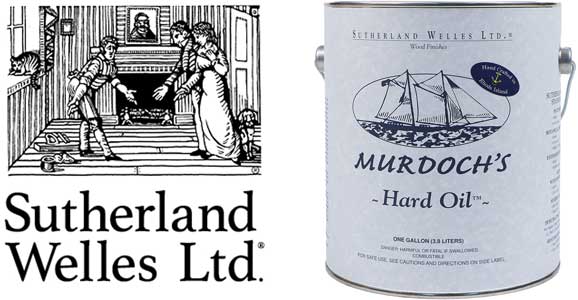
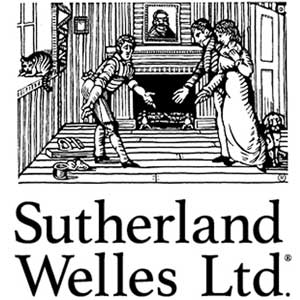
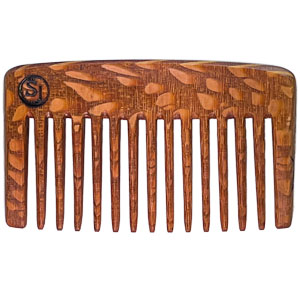
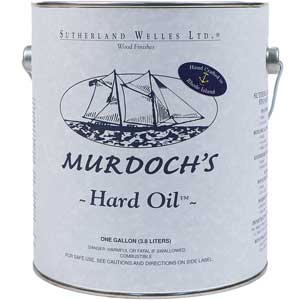
Sutherland Welles Murdoch's Hard Oil —a wiping varnish made with polymerized tung oil and uralkyd resin (the most durable of the resins and the best of the oils). I believe this is the best wood finish—It's what I use for SavvyJack products.
Varnish made with polymerized oil will cure harder and therefore provide more protection than varnish made with a standard curing oil.
Murdoch's Hard Oil can be applied and wiped after each coat to achieve great protection while retaining the natural wood look and feel.
-
Low sheen finish
- Wipe off all coats 20 minutes after application.
- More natural wood feel—the protective layer penetrates into the wood, but does not build much on top.
-
High sheen finish
- Don't wipe unabsorbed finish after each coat.
- Increase sheen further by polishing once fully cured.
Below you can see the application of four coats of Murdoch's on Black Walnut end-grain coasters. All coats were wiped, and the finish was buffed after the final coat.
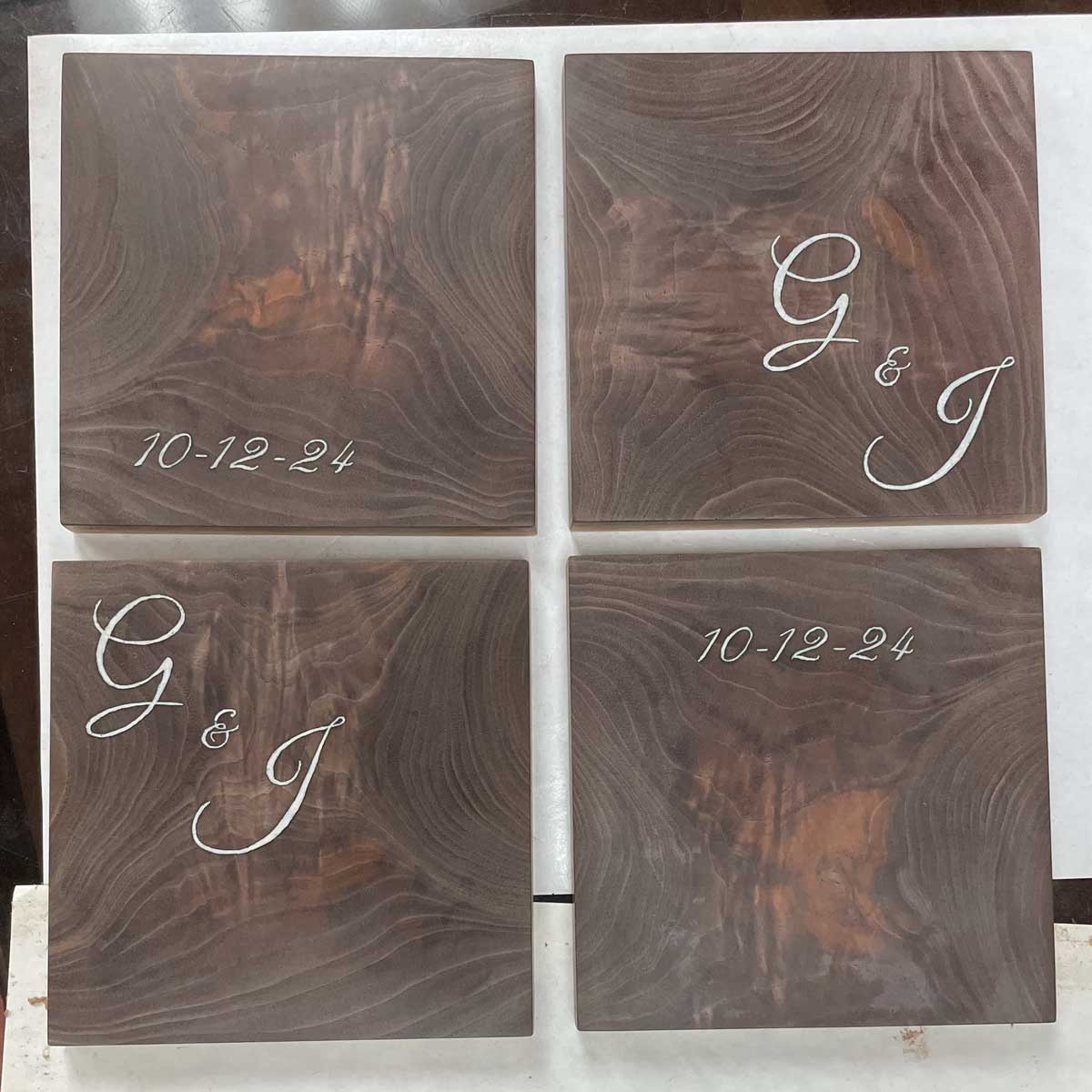
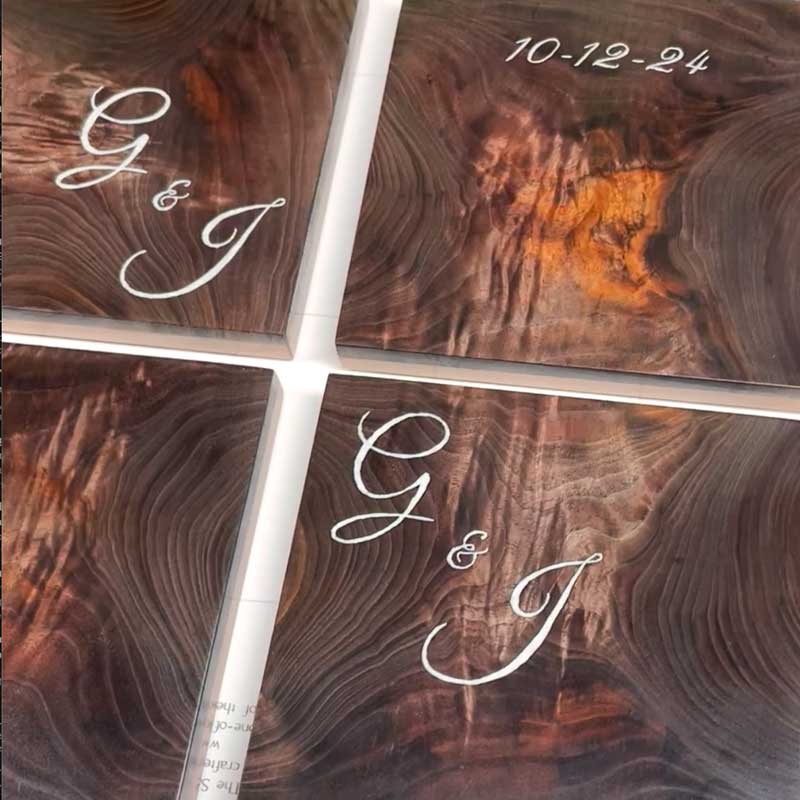
-
Protection & Longevity
- Best protection
- Hardness/flexibility varies
- Higher oil content makes a varnish more flexible to accommodate wood movement
-
Appearance
- Can be built up for a high sheen gloss
- Can be wiped away for low sheen
- Can't achieve a matte appearance as well as curing oils
-
Open working time
- Full strength varnishes cure quickly
- "Wiping varnishes" have long working times
2. Polymerized Oil
Polymerized oils are standard curing oils, like tung and linseed, that go through a heating process in an oxygen-free environment.
This process causes the oils to crosslink, but not oxidize. This decreases cure time and increases hardness making them a much more protective finish compared to standard curing oils.
Polymerized oils are hard enough to be built up as surface layers to achieve a gloss finish. This can't be done with standard curing oils as they cure to a softness that would remain gummy on the wood surface.
You can get it in low, medium, or high luster, as well as a botanical version which uses orange-peel citrus solvent instead of mineral spirits.
*Low luster has significantly more open working time than high luster.
-
Protection & Longevity
- Excellent protection/durability
- Flexible enough to accomodate wood movement
-
Appearance
- Softer and therefore less sheen than varnishes
- Harder and therefore more sheen than standard curing oils
-
Open working time
- Generally short
- Can be challenging to use on large surfaces
- Higher solvent content can prolong working time
3. Curing Oil
Curing oils "cure" or "dry" by a process called oxidative polymerization; certain fatty acids crosslink with each other in the presence of oxygen.
*This is different than the non-oxidative polymerization process used to make "polymerized oils".
The curing process hardens the oils, making them an effective wood finish.
Curing oils:
- Linseed (flax) oil, Tung oil, Hempseed oil, Perilla oil
Linseed and Tung cure the hardest and therefore offer the most protection
Semi-curing oils:
- Walnut oil, Soybean oil, Safflower oil, Sunflower oil
These don't make very good wood finishes. However, they are often chemically modified to fully cure. These modified semi-curing oils are often found in varnishes.
Non-curing oils
- Mineral oil, Olive oil and most other oils
These oils remain soft and therefore do not offer any protection. Mineral oil is a wood conditioner, not a finish.
Tung oil is a historically revered finish, but is very time-consuming to apply. You need 5-10 coats to achieve it's high water resistance (for an oil).
Tung oil cures slowly. You must wait several days between coats, and a month before heavy use.
The majority of finishes sold as "tung oil" have no tung oil content whatsoever. It's become a marketing trade name. Unless a finish specifically lists tung oil as an ingredient, assume it's a varnish or oil/varnish blend made with linseed, soybean or similar oils.
*These days, a polymerized tung oil is often the way to go.
Boiled linseed oil cures in a day—raw linseed oil takes weeks or months.
Boiled linseed oil is less water-resistant than tung oil, but requires fewer coats and cures faster.
The majority of finishes sold as "boiled linseed oil" (BLO) are not actually boiled like they once were. Instead, they have added catalysts called "driers" to hasten the curing process.
These driers cause linseed to cure in about a day instead of a month or more, making them a much better finish.
*Linseed is another name for flaxseed. Linseed is used in industrial contexts, while flaxseed is used in the context of food. Probably a smart move as you wouldn't want to consume industrial linseed oil.
Most "oil" finishes sold today are not oil, but varnishes or oil/varnish blends.
They go by names like:
- Teak Oil, Danish Oil, Antique Oil and even Tung Oil
Though it's misleading, these are actually better finishes than a simple oil. But if you're looking for an oil, these aren't it.
-
Protection & Longevity
- Low protection—much less than varnishes or polymerized oils
- Very flexible—no issues with wood movement
-
Appearance
- Matte
- Not hard enough to build up a sheen layer.
- Can, however, be polished afterwards with a wax.
-
Open working time
- Very long—easy to use
- Take several weeks to fully cure and protect
4. Lacquer
Lacquer is an evaporative finish. Unlike the curing process of varnish where chemical bonds form between molecules, the resin molecules in evaporative finishes simply coalesce together as the solvents evaporate.
Though it contains hard resins like varnish, the resins do not chemically crosslink. The bond between molecules is therefore weaker, and the resistance to water, wear, heat and solvents is correspondingly decreased.
These two finishes are a binder plus the same range of hard resins. It seems the binder must make the difference.
The binders in lacquers are nitrocellulose, acrylic or both. The binders in varnish are curing oils.
-
Varnish cures
- The molecules chemically crosslink with each other.
- Once cured, it cannot easily be redissolved.
-
Lacquer evaporates
- The binder and resin molecules conentrate into a hard film with no remaining liquid, but do not chemically bind with each other as far as I know—certianly not to the extent of varnish.
- Dried, hard lacquer is readily redisolved with solvent.
- This means they're damaged by solvents.
- This also means they're easily repairable.
Of course, lacquer is very popular because it also has many desirable qualities...
- Fast drying time
- Excellent depth and clarity
- Can be applied in a wide temperature range
- Great repairability
- Vulnerability to solvents has a plus side—because lacquer redissolves in lacquer solvent, you can easily repair or even remove the finish later.
- Highly versatile
- Many different resin and solvent combinations are available as well as a variety of additives that further adapt its properties.
- Excellent sprayability
- In the professional setting, lacquers are almost always sprayed. It is this method which most fully takes advantage of the beneficial characteristics of lacquer.
*Though none of the petroleum-based wood finish solvents are good for you, lacquer contains a large number of solvents—some of them are particularly harmful, and lacquer is generally considered to have the most harmful fumes of any wood finish category.
-
Protection & Longevity
- Less protection than varnish
- More protection than standard curing oils
- Plasticizers can be added to enhance flexibility and accomodate wood movement
-
Appearance
- Comes in full range of sheens
- It's a film finish, so the feel of the wood is "plasticky" similar to building up several layers of varnish
-
Open working time
- Very short
- Typically sprayed rather than brushed, though there are some brushing lacquers with increased working time.
- Easy to apply to vertical surfaces without runs
- Less time for dust to ruin a finish
5. Water Base
- aka 'water-based' / 'waterborne'
Water-based finishes coalesce as they evaporate like lacquer, as opposed to curing like varnish. However, unlike lacquer’s individual resin molecules, water base has larger droplets of pre-crosslinked resin.
If lacquer is like solidified sand, water base is like solidified gravel. This makes water-based finishes more scratch resistant than lacquer, yet still less scratch resistant than varnish which crosslinks fully.
Generally speaking, water base and lacquer have equivalent water, heat, and solvent resistance. Varnish is better in all of these categories as well.
Water base finishes are not solvent free:
- They contain both water and as much as 20% glycol ether.
- Lacquer solvents are much more volatile petrochemicals.
Glycol ether evaporates slower than water. Therefore, as the water evaporates, the glycol ether becomes more concentrated.
This concentrated glycol ether makes the hard resin droplets sticky, enabling them to bond with each other.
As the remaining glycol ether completely evaporates, the resins coalesce into a hard, protective layer.
The primary reason for the development of water-based finishes is to avoid the more noxious solvents in traditional finishes. This is driven both by government regulation as well as consumer preference.
Water-based finishes are often called "polyurethane" or "varnish." To determine what type of finish it is, look at the ingredients and recommended thinners/solvents. If you see mineral spirits, petroleum distillate, paint thinner, naphtha or the like, it is not water-based. If you see water, it is.
-
Protection & Longevity
- Overall good protection level:
- Equal or better than lacquer.
- Worse than varnish.
- Good scratch and water resistance.
- Poor solvent and heat resistance.
-
Appearance
- Can be built up to achive high sheen levels
- Adds very little color to the wood.
- Great when you want to keep white woods white.
- Looks a bit cold on dark woods unless a warm colorant is added.
-
Open working time
- Gernally longer than lacquer, but shorter than varnish.
6. Wax
Wax as a standalone finish provides very little protection, and hence has been displaced in modern times with the other finishes in this article.
Wax makes a good polish to be used on top of other, more protective finishes. The harder the wax, the higher the sheen.
-
Montan (Lignite)
- Very Hard
- Melting point: 180-203F
-
Carnauba
- Very Hard
- Melting point: 180-187F
-
Candelilla
- Hard
- Melting point: 154-163F
-
Beeswax
- Moderate to Hard
- Melting point: 144-149F
-
Paraffin
- Soft to Moderate
- Melting point: 120-160F
Paste wax is a wax dissolved in a solvent. This makes the wax easy to apply—the solvent evaporates, and only the wax is left.
It is often used for treating/polishing wooden floors. I use it to prevent rust and reduce friction on the table surfaces of my woodworking machinery.
Products such as Howard Butcher Block Conditioner are meant to be used very frequently. They condition the wood, preventing drying and cracking.
The wax content (beeswax and carnauba in the case of Howard) offers some, but little protection compared to the other wood finishes.
-
Protection & Longevity
- Offers very little protection
- Better applied as a polish over other finishes than used as a standalone finish
- Flexible–no issues with wood movement
-
Appearance
- Full range of sheens achievable
- Starts matte–can be polished to high gloss
-
Open working time
- Paste wax: Fairly short—add solvent to increase
- Wax+oil: very long (Butcher block conditioner)
A note on Sutherland Welles
You've likely noticed that I've found a liking for Sutherland Welles' finishes. I now use them exclusively for my SavvyJack products.
I have no affiliation with the company—I'm a satisfied customer sharing what I find to be effective.
For detailed application instructions on the Sutherland Welles site, scroll down on each of their product pages. They also have a substantial FAQ.
If you're curious, you can check out some of the handcrafted wooden grooming products I make in The SavvyJack Shop or via the links below.
Thanks for reading!
You've likely noticed that I've grown quite fond of Sutherland Welles finishes. I now use them exclusively for my SavvyJack products.
I have no affiliation with the company—I'm just a happy customer!
For detailed application instructions on the Sutherland Welles site, scroll down on each product page. They also have a substantial FAQ.
If you're curious, you can check out some of the handcrafted wooden grooming products I make in The SavvyJack Shop or the links below.
SavvyJack Productions
Wood Finish:
Sutherland Welles Murdoch's Hard Oil
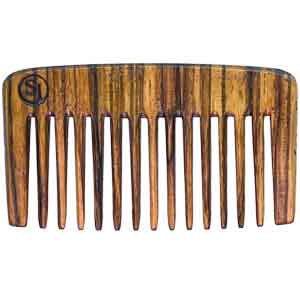
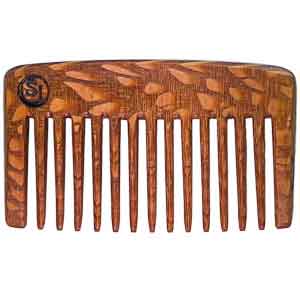
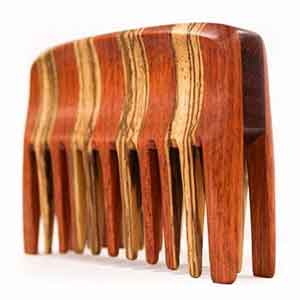
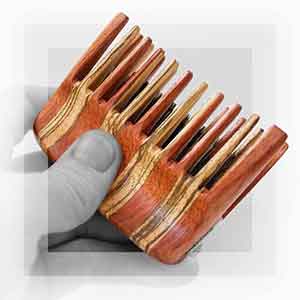
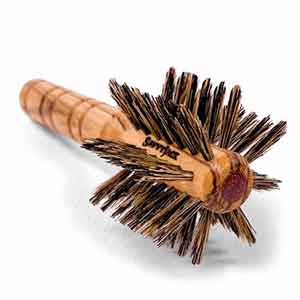
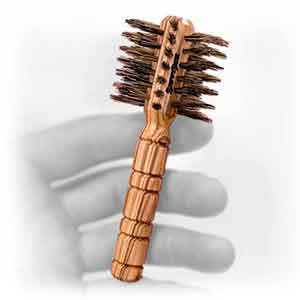
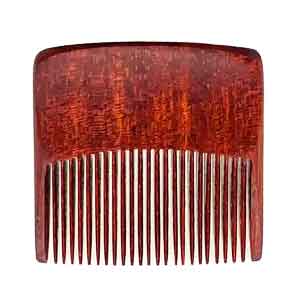
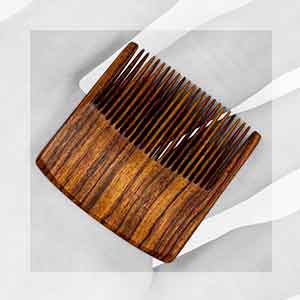
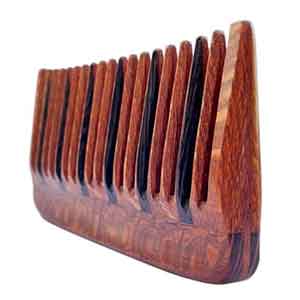
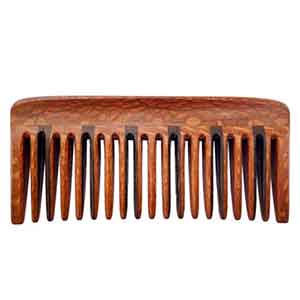